In PET preform injection molding, controlling the moisture content of raw materials is critical to ensuring product quality. PET is highly sensitive to moisture. If not properly dried, it can lead to hazy preforms, bubbles, brittleness, and ultimately reduced transparency and mechanical strength. Therefore, selecting a reliable and efficient dehumidifying dryer is essential for producing high-quality PET preforms.
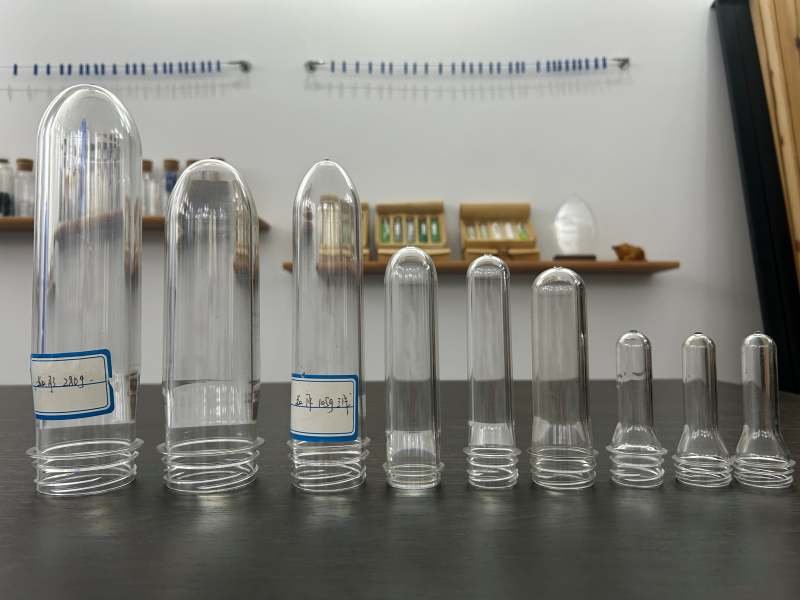
1. PET Preform Production Overview
Below are the core parameters of a typical PET preform injection molding line:
- Raw material consumption: 432 kg/hour
- Preform output: 2,618 pieces/hour
- Mold cavities: 24
- Single preform weight: 165g
- Injection cycle: 33 seconds
Most PET processors today use pre-crystallized PET pellets, which means pre-crystallization is not required. These materials can be directly dried using a high-performance dehumidifying dryer.
2. PET Preform Drying Requirements & Configuration Basis
To meet injection molding standards, PET must be dried to a moisture content of 0.005% or less. Conventional hot air dryers cannot achieve this level, making dedicated dehumidifying dryers a necessity.
In practice, however, the initial moisture content of raw materials is often uncertain:
- If the material is relatively dry, 3–4 hours of drying may be sufficient.
- If the material has absorbed more moisture, and considering possible delays in manual loading, it is safer to configure the system for 6 hours of drying capacity.
Based on this, a dryer should support at least 2,592 kg of PET material (432 kg/h × 6 hours).
3. Recommended Equipment Comparison
Fyndax recommends the following two high-performance dryers to match this production requirement:
✅ FXD-PET3200 (Recommended Primary Option)
- Drying airflow: 1300 m³/h
- Drying hopper volume: 3200L
- Maximum PET loading capacity: 2500KG
- Total energy consumption at 160°C: Approx. 60℃/H
- Dew point control: Precise and stable between -45℃ to -70℃, unaffected by environment or material fluctuations
- Advantages:
- Excellent drying uniformity
- Energy-efficient and cost-saving
- Highly stable temperature and dew point control
- Ideal for: High-end manufacturers with strict quality control standards
FXD-F-PET3200
- Drying airflow: 1500 m³/h
- Drying hopper volume: 3200L
- Maximum PET loading capacity: 2500KG
- Total energy consumption at 160°C: Approx. 95℃/H
- Dew point control: Typically maintained at -45℃, but subject to fluctuations due to weather and material moisture content
- Advantages:
- Lower initial investment
- Fast drying speed, suitable for fast-paced production
- Ideal for: Cost-sensitive operations with moderate quality requirements
4. Summary & Selection Recommendations
In PET preform production, dryer selection must consider both drying capacity and dew point stability, in addition to energy efficiency.
Comparison | FXD-PET3200 | FXD-F-PET3200 |
---|---|---|
Max. PET Load | 2500KG | 2500KG |
Energy Consumption | ≈60℃/H (Energy-saving) | ≈95℃/H (Higher usage) |
Dew Point Control | -45℃ to -70℃, highly stable | ~-45℃, more fluctuation |
Environmental Adaptability | Excellent, consistent results | Sensitive to weather/material |
Suitable For | High-end, quality-focused production | SMEs, cost-driven production |
Recommendation:
- For customers focused on product consistency and operational efficiency, we recommend FXD-PET3200.
- For operations with tighter budgets and less emphasis on dew point precision, FXD-F-PET3200 may suffice.
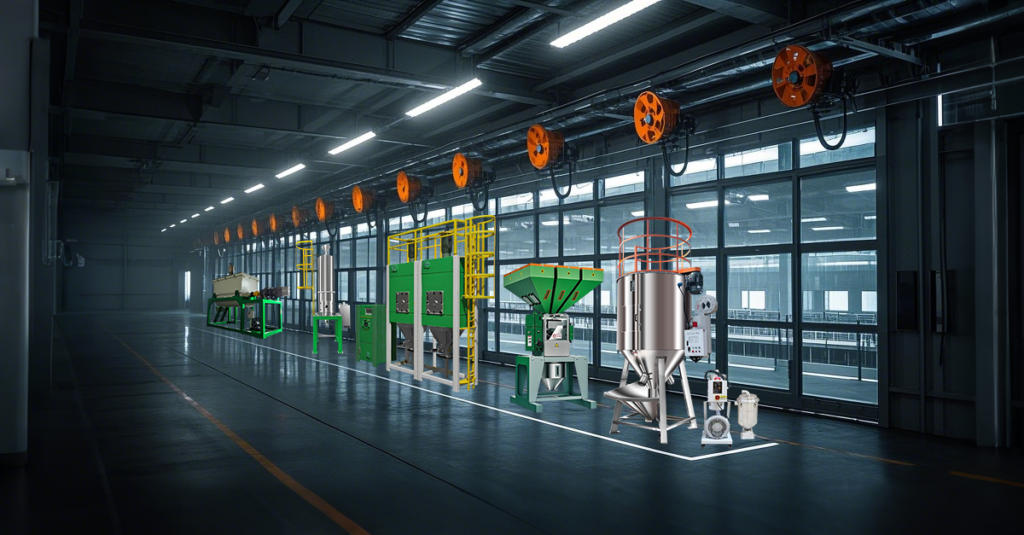
5. What Fyndax Offers
Fyndax is committed to delivering high-performance, energy-efficient, and dew point-controlled dehumidifying drying solutions for the PET preform industry. From equipment selection to on-site commissioning and after-sales support, we provide complete technical solutions tailored to your needs—helping you improve product quality and reduce operational costs.
Need personalized configuration advice or trial testing? Contact us today to get your tailored drying solution.